Sustainability
WHAT MAKES BOYISH JEANS SO SPECIAL?
Our Fabrics, And our true
transparency into our unique
non-toxic process.
"Our Fabrics, And our true transparency into our unique non-toxic process."
Sustainability is at
the core of our fabric
DYSTAR INDIGO
We use reduced indigo from Dystar with about 80 percent less sulphates.
NATURAL PLANT BASED DYES
We’ve reduced the hazardous impacts of synthetic dyes by choosing plant based dyes instead. Plant based dyes not only reduce the toxins you put on your skin, they come in a range of alluring colors.
WATER PROTECTION
We recycle water to keep harsh chemicals out of fresh-water streams. We work with fabric mills and factories around the world that are part of the ZDHC Program, Roadmap to Zero, where they collaboratively advance the field of water safety in the textile and apparel industries.
FEWER DRIPS
We dip our fabric fewer times to conserve energy and water.
Our non-
toxic dyes and
gentle processes
protect water,
keeping it safe
for people and
the environment.
OEKO-TEX STANDARD 100 APPROVED
Our textile safety is verified by Oeko-Tex. Its Standard 100 goes beyond national and international standards for protection from harmful toxins, chemicals, dyes and restricted substances (both MSRL and RSL). We ensure our textiles are ecologically safe and healthy for humans.
DYSTAR INDIGO
We use reduced indigo from Dystar with about 80 percent less sulphates.
NATURAL PLANT BASED DYES
We’ve reduced the hazardous impacts of synthetic dyes by choosing plant based dyes instead. Plant based dyes not only reduce the toxins you put on your skin, they come in a range of alluring colors.
WATER PROTECTION
We recycle water to keep harsh chemicals out of fresh-water streams. We work with fabric mills and factories around the world that are part of the ZDHC Program, Roadmap to Zero, where they collaboratively advance the field of water safety in the textile and apparel industries.
FEWER DRIPS
We dip our fabric fewer times to conserve
energy and water.
Our non-
toxic dyes and
gentle processes
protect water,
keeping it safe
for people and
the environment.
Our non-
toxic dyes and
gentle processes
protect water,
keeping it safe
for people and
the environment.
OEKO-TEX STANDARD 100 APPROVED
Our textile safety is verified by Oeko-Tex. Its Standard 100 goes beyond national and international standards for protection from harmful toxins, chemicals, dyes and restricted substances (both MSRL and RSL). We ensure our textiles are ecologically safe and healthy for humans.
DYSTAR INDIGO
We use reduced indigo from Dystar with
about 80 percent less sulphates.
Our non-
toxic dyes and
gentle processes
protect water,
keeping it safe
for people and
the environment.
NATURAL PLANT BASED DYES
We’ve reduced the hazardous impacts of synthetic dyes by choosing plant based dyes instead. Plant based dyes not only reduce the toxins you put on your skin, they come in a range of alluring colors.
WATER PROTECTION
We recycle water to keep harsh chemicals out of fresh-water streams. We work with fabric mills and factories around the world that are part of the ZDHC Program, Roadmap to Zero, where they collaboratively advance the field of water safety in the textile and apparel industries.
FEWER DRIPS
We dip our fabric fewer times to conserve
energy and water.
Let's
Talk
Tencel
Let's
Talk
Tencel
We source
eco-friendly
fabrics to
reduce waste
and eliminate
synthetics.
CANDIANI DENIM (Weaving Mill)
Candiani Denim is a pioneering denim fabric mill renowned for its commitment to innovation and sustainability. Situated within the Parco del Ticino Nature Reserve, the company has a rich history of eco-friendly practices, dating back to the 1970s. From water conservation to the development of compostable stretch denim technology, Candiani has consistently pushed the boundaries of responsible denim production. Their dedication to transparency and responsible manufacturing sets them apart as a leader in sustainable fashion within the denim industry.
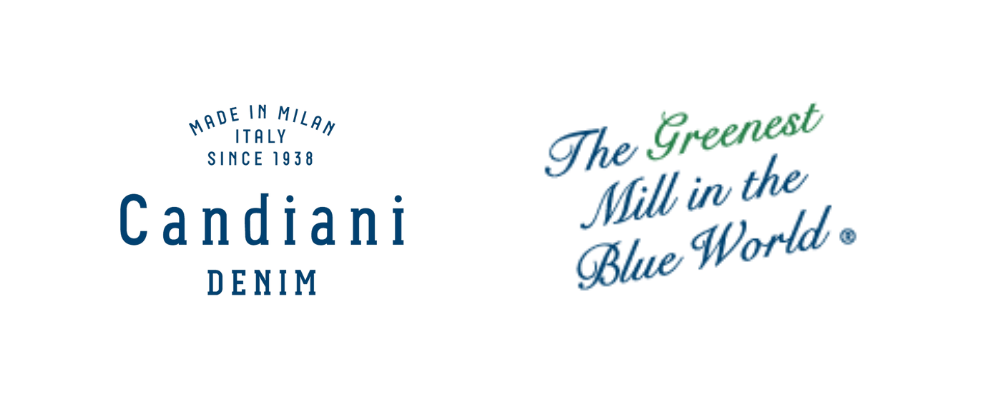
OCS 100 CERTIFIED ORGANIC COTTON
The Organic Content Standard (OCS Certified) is a standard for tracking and verifying the content of organically grown materials in a final product.
RECYCLED COTTON
This material requires no water to make jeans. Recycled cotton is also the most sustainable cotton fiber source according to the Sustainable Apparel Coalition’s Higg Index.
GRS RECYCLED FABRICS
The sustainable recycled content of our fabric is third-party certified.
DEADSTOCK FABRICS
We hunt for vintage rolls of fabric that never made the cut. Making clothes from deadstock fabric saves about 10,000 pounds of CO2 emissions each year.
TENCEL™ LYOCELL
Put this fabric on your radar. It is one of the most sustainable options right now. It’s made of sustainable wood pulp from eucalyptus trees that are FSC certified, so they’re not sourced from rainforests. Compared to traditional cotton, Tencel™ uses just a fifth of the land and a tenth of the water to produce, thanks to its closed-loop manufacturing process.
TENCEL™ X REFIBRA LYOCELL
Why not blend some recycled cotton in with your TENCEL TM Lyocell? We have innovated by adopting the closed loop Lyocell manufacturing process to keep cotton scraps out of the landfill.
We source
eco-friendly
fabrics to
reduce waste
and eliminate
synthetics.
VEGAN DENIM
Our jeans are cruelty-free and PETA approved. We use absolutely zero leather or animal products in our garments and accessories.
OCS 100 CERTIFIED ORGANIC COTTON
The Organic Content Standard (OCS Certified) is a standard for tracking and verifying the content of organically grown materials in a final product.
RECYCLED COTTON
This material requires no water to make jeans. Recycled cotton is also the most sustainable cotton fiber source according to the Sustainable Apparel Coalition’s Higg Index.
GRS RECYCLED FABRICS
The sustainable recycled content of our fabric is third-party certified.
DEADSTOCK FABRICS
We hunt for vintage rolls of fabric that never made the cut. Making clothes from deadstock fabric saves about 10,000 pounds of CO2 emissions each year.
TENCEL™ LYOCELL
Put this fabric on your radar. It is one of the most sustainable options right now. It’s made of sustainable wood pulp from eucalyptus trees that are FSC certified, so they’re not sourced from rainforests. Compared to traditional cotton, Tencel™ uses just a fifth of the land and a tenth of the water to produce, thanks to its closed-loop manufacturing process.
TENCEL™ X REFIBRA LYOCELL
Why not blend some recycled cotton in with your TENCEL TM Lyocell? We have innovated by adopting the closed loop Lyocell manufacturing process to keep cotton scraps out of the landfill.
Disclaimer: TENCEL™, REFIBRA
are trademarks of Lenzing AG
Our jeans
are made for
longevity.
Our jeans
are made for
longevity.
VINTAGE-INSPIRED
Boyish jeans are inspired by classic vintage jeans that last for decades without losing their great fit and style.
LONG LIFESPAN
By minimizing plastic fibers in our designs, we’ve extended the lifespan of our jeans. We replace traditional plastic fibers with fibers like Refibra™, which is biodegradable, non-toxic and also antimicrobial.
DURABLE
Our all-natural jeans contain thicker material blended with Tencel, which makes them strong and durable. As members of The Jeans Redesign project from the Ellen MacArthur Foundation, we embrace circular economy guidelines by making durable products, not disposable ones.
RECYCLABLE JEANS
Diverting waste from landfills starts at the product design phase. We’ve designed our jeans to be recycled into new products at the end of their life. To learn more about bringing circular design into our daily lives, read Cradle to Cradle by William McDonough.
VINTAGE-INSPIRED
Boyish jeans are inspired by classic vintage jeans that last for decades without losing their great fit and style.
LONG LIFESPAN
By minimizing plastic fibers in our designs, we’ve extended the lifespan of our jeans. We replace traditional plastic fibers with fibers like Refibra™, which is biodegradable, non-toxic and also antimicrobial.
DURABLE
Our all-natural jeans contain thicker material blended with Tencel, which makes them strong and durable. As members of The Jeans Redesign project from the Ellen MacArthur Foundation, we embrace circular economy guidelines by making durable products, not disposable ones.
RECYCLABLE JEANS
Diverting waste from landfills starts at the product design phase. We’ve designed our jeans to be recycled into new products at the end of their life. To learn more about bringing circular design into our daily lives, read Cradle to Cradle by William McDonough.
Ethical washing makes
a huge impact
Ethical washing makes
a huge impact
Ethical washing makes a huge impact
Neutral enzymes
We use neutral enzymes made by Dystar in cold water, not pumice stone. This reduces waste and the use of natural resources. Most of our eco-friendly chemicals are all third party certified and approved.
Cold Water
Not only do we wash in cold water, we recommend you do, too. Check our label.
laser machine finishing
In our finishing process, we scrape with laser machines. They take up less space than hand-scraping; hence, less energy. Thanks to Jeanlogia and VAV Technologies machines, we maximize water and energy efficiency, reduce chemicals and ensure safety.
vapor water
Using Tonello’s All-in-One machines, we wash with vapor water to save water and energy. For that stone-washed look, we use nano bubbles to cut down on harsh chemicals. We swear, none of this is science fiction.
ozone wash
We “bleach” without hypo-chloride bleach. Instead, we use triple-molecule Oxygen (O3). In the industry we call it Ozone Wash.
Faux STONE WASH
Traditional stone washing uses natural pumice stone. Mining this stone generates high carbon emissions and it has a negative impact on the earth. When it’s used in the stone washing process, pumice breaks down, creating a sludge that makes the water unrecyclable. We use faux stones that are not mined from the earth and create zero waste so that all our water can be recycled.
no pp
To cut back on yet another harsh chemical, we use a natural enzyme made by Nearchimica instead of PP (potassium permaganate) to get that vintage vibe. It also saves water by eliminating the PP neutralizing process.
Neutral enzymes
We use neutral enzymes made by Dystar in cold water, not pumice stone. This reduces waste and the use of natural resources. Most of our eco-friendly chemicals are all third party certified and approved.
Cold Water
Not only do we wash in cold water, we recommend you do, too. Check our label.
laser machine finishing
In our finishing process, we scrape with laser machines. They take up less space than hand-scraping; hence, less energy. Thanks to Jeanlogia and VAV Technologies machines, we maximize water and energy efficiency, reduce chemicals and ensure safety.
Neutral enzymes
We use neutral enzymes made by Dystar in cold water, not pumice stone. This reduces waste and the use of natural resources. Most of our eco-friendly chemicals are all third party certified and approved.
Cold Water
Not only do we wash in cold water, we recommend you do, too. Check our label.
laser machine finishing
In our finishing process, we scrape with laser machines. They take up less space than hand-scraping; hence, less energy. Thanks to Jeanlogia and VAV Technologies machines, we maximize water and energy efficiency, reduce chemicals and ensure safety.
vapor water
Using Tonello’s All-in-One machines, we wash with vapor water to save water and energy. For that stone-washed look, we use nano bubbles to cut down on harsh chemicals. We swear, none of this is science fiction.
ozone wash
We “bleach” without hypo-chloride bleach. Instead, we use triple-molecule Oxygen (O3). In the industry we call it Ozone Wash.
faux stone wash
Traditional stone washing uses natural pumice stone. Mining this stone generates high carbon emissions and it has a negative impact on the earth. When it’s used in the stone washing process, pumice breaks down, creating a sludge that makes the water unrecyclable. We use faux stones that are not mined from the earth and create zero waste so that all our water can be recycled.
no pp
To cut back on yet another harsh chemical, we use a natural enzyme made by Nearchimica instead of PP (potassium permaganate) to get that vintage vibe. It also saves water by eliminating the PP neutralizing process.
Neutral enzymes
We use neutral enzymes made by Dystar in cold water, not pumice stone. This reduces waste and the use of natural resources. Most of our eco-friendly chemicals are all third party certified and approved.
Cold Water
Not only do we wash in cold water, we recommend you do, too. Check our label.
laser machine finishing
In our finishing process, we scrape with laser machines. They take up less space than hand-scraping; hence, less energy. Thanks to Jeanlogia and VAV Technologies machines, we maximize water and energy efficiency, reduce chemicals and ensure safety.
Neutral enzymes
We use neutral enzymes made by Dystar in cold water, not pumice stone. This reduces waste and the use of natural resources. Most of our eco-friendly chemicals are all third party certified and approved.
Cold Water
Not only do we wash in cold water, we recommend you do, too. Check our label.
laser machine finishing
In our finishing process, we scrape with laser machines. They take up less space than hand-scraping; hence, less energy. Thanks to Jeanlogia and VAV Technologies machines, we maximize water and energy efficiency, reduce chemicals and ensure safety.
vapor water
Using Tonello’s All-in-One machines, we wash with vapor water to save water and energy. For that stone-washed look, we use nano bubbles to cut down on harsh chemicals. We swear, none of this is science fiction.
ozone wash
We “bleach” without hypo-chloride bleach. Instead, we use triple-molecule Oxygen (O3). In the industry we call it Ozone Wash.
faux stone wash
Traditional stone washing uses natural pumice stone. Mining this stone generates high carbon emissions and it has a negative impact on the earth. When it’s used in the stone washing process, pumice breaks down, creating a sludge that makes the water unrecyclable. We use faux stones that are not mined from the earth and create zero waste so that all our water can be recycled.
no pp
To cut back on yet another harsh chemical, we use a natural enzyme made by Nearchimica instead of PP (potassium permaganate) to get that vintage vibe. It also saves water by eliminating the PP neutralizing process.
Why we take third-party certifications seriously
Why we take third-party certifications seriously
Imagine booking an airline ticket only to discover that your flight is scheduled on an airplane with defective parts. Would you want to step foot on that airplane? Probably not.
You soon learn the reason for this: the airplane’s safety was only checked by the airplane’s manufacturer, so the defective parts had no third-party approval. (This may sound familiar.)
The same goes for testing the materials and dyes used in the pieces of clothing we wear each day. You should definitely look for third-party certifications.
Think about it. Clothing is one of the most intimate things we own. It stays in constant contact with the largest organ of our bodies: our skin.
Yet, the fashion industry has been slow to update its practices. The chemicals, fibers and processes used to make our clothing are not always tested or verified for safety. Or when they are tested, the standards are way too low.
That’s why we back up nearly every sustainable improvement we make with third-party certifications. This holds our brand to a truly sustainable standard while building your trust.
Imagine booking an airline ticket only to discover that your flight is scheduled on an airplane with defective parts. Would you want to step foot on that airplane? Probably not.
You soon learn the reason for this: the airplane’s safety was only checked by the airplane’s manufacturer, so the defective parts had no third-party approval. (This may sound familiar.)
The same goes for testing the materials and dyes used in the pieces of clothing we wear each day. You should definitely look for third-party certifications.
Think about it. Clothing is one of the most intimate things we own. It stays in constant contact with the largest organ of our bodies: our skin.
Yet, the fashion industry has been slow to update its practices. The chemicals, fibers and processes used to make our clothing are not always tested or verified for safety. Or when they are tested, the standards are way too low.
That’s why we back up nearly every sustainable improvement we make with third-party certifications. This holds our brand to a truly sustainable standard while building your trust.
Sustainable
Never Looked
So Good
Almost nothing
goes to waste
Almost nothing
goes to waste
When we set zero waste as our goal, we decided to look at the details. Every zipper, thread and stitch is an opportunity to innovate.
Trace
our
materials.
Recycled cuttings
We recycle all of our cutting waste: some goes back into our new fabrics and the rest gets recycled for industrial uses.
Closed-Loop tech
Thanks to the closed-loop technology of Re:Newcell, we recycle all our stretch fabrics.
Recycled paper
Our hang tags are made with recycled paper.
Recycled Metal
We use recycled metal in our buttons, rivets and other hardware.
Recycled LABELS
We make our labels and tags from recycled materials.
PLANT BASED SHIPPING BAGS
We ship our products in 100 percent compostable shipping bags that break down in less than a year. Traditional polybags take up to 200 years or more to decompose.
When we set zero waste as our goal, we decided to look at the details. Every zipper, thread and stitch is an opportunity to innovate.
Trace
our
materials.
Circular Economy
As members of The Jeans Redesign project from the Ellen MacArthur Foundation, we’ve joined the circular economy. The project guidelines ensure that we create durable jeans made with recyclable, traceable materials and minimal pollution.
Recycled cuttings
We recycle all of our cutting waste: some goes back into our new fabrics and the rest gets recycled for industrial uses.
Closed-Loop tech
Thanks to the closed-loop technology of Re:Newcell, we recycle all our stretch fabrics.
Recycled paper
Our hang tags are made with recycled paper.
Recycled Metal
We use recycled metal in our buttons, rivets and other hardware.
Recycled LABELS
We make our labels and tags from recycled materials.
PLANT BASED SHIPPING BAGS
We ship our products in 100 percent compostable shipping bags that break down in less than a year. Traditional polybags take up to 200 years or more to decompose.
When we set zero waste as our goal, we decided to look at the details. Every zipper, thread and stitch is an opportunity to innovate.
Circular Economy
As members of The Jeans Redesign project from the Ellen MacArthur Foundation, we’ve joined the circular economy. The project guidelines ensure that we create durable jeans made with recyclable, traceable materials and minimal pollution.
Recycled cuttings
We recycle all of our cutting waste: some goes back into our new fabrics and the rest gets recycled for industrial uses.
Closed-Loop tech
Thanks to the closed-loop technology of Re:Newcell, we recycle all our stretch fabrics.
Recycled paper
Our hang tags are made with recycled paper.
Recycled Metal
We use recycled metal in our buttons, rivets and other hardware.
Recycled LABELS
We make our labels and tags from recycled materials.
PLANT BASED SHIPPING BAGS
We ship our products in 100 percent compostable shipping bags that break down in less than a year. Traditional polybags take up to 200 years or more to decompose.
When we set zero waste as our goal, we decided to look at the details. Every zipper, thread and stitch is an opportunity to innovate.
Trace
our
materials.
Circular Economy
As members of The Jeans Redesign project from the Ellen MacArthur Foundation, we’ve joined the circular economy. The project guidelines ensure that we create durable jeans made with recyclable, traceable materials and minimal pollution.
Recycled cuttings
We recycle all of our cutting waste: some goes back into our new fabrics and the rest gets recycled for industrial uses.
Closed-Loop tech
Thanks to the closed-loop technology of Re:Newcell, we recycle all our stretch fabrics.
Recycled paper
Our hang tags are made with recycled paper.
Recycled Metal
We use recycled metal in our buttons, rivets and other hardware.
Recycled LABELS
We make our labels and tags from recycled materials.
PLANT BASED SHIPPING BAGS
We ship our products in 100 percent compostable shipping bags that break down in less than a year. Traditional polybags take up to 200 years or more to decompose.
View
footage
from
our
most
recent
trip.
CODE OF CONDUCT
All of our suppliers must sign our Code of Conduct before our working relationship begins.
HONEST WAGES
All of our factories pay average wages over the minimum wage. We are striving to ensure 100% of our workers earn living wages. We joined the Lowest Wage Challenge to motivate others that worker compensation transparency is extremely important.
in-person visits
We take annual trips to our factories and the farms where we source our organic cotton to meet the people who craft our jeans.
third-party audits
We also conduct third party audits up and down our supply chain to meet our high social responsibility and environmental standards. Find out more about Intertek, the company we've partnered with to ensure Boyish Jeans are made ethically.
By choosing factories that have fair, safe and healthy working conditions, we support employers providing meaningful jobs.
View
footage
from
our
most
recent
trip.
CODE OF CONDUCT
All of our suppliers must sign our Code of Conduct before our working relationship begins.
honest WAGES
All of our factories pay average wages over the minimum wage. We are striving to ensure 100% of our workers earn living wages. We joined the Lowest Wage Challenge to motivate others that worker compensation transparency is extremely important.
in-person visits
We take annual trips to our factories and the farms where we source our organic cotton to meet the people who craft our jeans.
third-party audits
We also conduct third party audits up and down our supply chain to meet our high social responsibility and environmental standards. Find out more about Intertek, the company we've partnered with to ensure Boyish Jeans are made ethically.
By choosing factories
that have fair, safe
and healthy working conditions, we support employers providing meaningful jobs.
CODE OF CONDUCT
All of our suppliers must sign our Code of Conduct before our working relationship begins.
honest WAGES
All of our factories pay average wages over the minimum wage. We are striving to ensure 100% of our workers earn living wages. We joined the Lowest Wage Challenge to motivate others that worker compensation transparency is extremely important.
in-person visits
We take annual trips to our factories and the farms where we source our organic cotton to meet the people who craft our jeans.
third-party audits
We also conduct third party audits up and down our supply chain to meet our high social responsibility and environmental standards. Find out more about Intertek, the company we've partnered with to ensure Boyish Jeans are made ethically.
By choosing factories that have fair, safe and healthy working conditions, we support employers providing meaningful jobs.
CODE OF CONDUCT
All of our suppliers must sign our Code of Conduct before our working relationship begins.
honest WAGES
All of our factories pay average wages over the minimum wage. We are striving to ensure 100% of our workers earn living wages. We joined the Lowest Wage Challenge to motivate others that worker compensation transparency is extremely important.
in-person visits
We take annual trips to our factories and the farms where we source our organic cotton to meet the people who craft our jeans.
third-party audits
We also conduct third party audits up and down our supply chain to meet our high social responsibility and environmental standards. Find out more about Intertek, the company we've partnered with to ensure Boyish Jeans are made ethically.
By choosing factories that have fair, safe and healthy working conditions, we support employers providing meaningful jobs.
Our supply chain is smart, simple, and transparent
Our supply chain is smart, simple, and transparent
Oftentimes, supply chains in fashion are overly complex, which can make it nearly impossible to trace and verify a company's environmental and labor standards. In contrast, we keep our supply chain simple.
Oftentimes, supply chains in fashion are overly complex, which can make it nearly impossible to trace and verify a company's environmental and labor standards. In contrast, we keep our supply chain simple.
Oftentimes, supply chains in fashion are overly complex, which can make it nearly impossible to trace and verify a company's environmental and labor standards. In contrast, we keep our supply chain simple.
Oftentimes, supply chains in fashion are overly complex, which can make it nearly impossible to trace and verify a company's environmental and labor standards. In contrast, we keep our supply chain simple.
short trips between facilities
We use nearby facilities to minimize our carbon emissions from transport.
regionally close production
Our production is limited to a small geographic region, mostly in Turkey. We source our organic cotton from Izmir, ship it to mills in Adana, and sew our jeans in a factory in Istanbul. We use Tencel™ yarns from a nearby manufacturer in Austria. We then send all our cutting scraps from Istanbul back to Adana to be recycled back into our factories closing the loop.
gots certified facilities
All of our mills and laundries are certified by GOTS for achieving high organic textile and chemical standards.
non-gmo cotton
By sourcing our natural fibers from Izmir, we ensure the use of non-GMO cotton, because Turkey restricts the use of GMO seeds in agriculture.
View our full list of factory
certifications
short trips between facilities
We use nearby facilities to minimize our carbon emissions from transport.
gots certified facilities
All of our mills and laundries are certified by GOTS for achieving high organic textile and chemical standards.
regionally close production
Our production is limited to a small geographic region, mostly in Turkey. We source our organic cotton from Izmir, ship it to mills in Adana, and sew our jeans in a factory in Istanbul. We use Tencel™ yarns from a nearby manufacturer in Austria. We then send all our cutting scraps from Istanbul back to Adana to be recycled back into our factories closing the loop.